Features and Applications
Cobalt base tubular wire for gas-shielded metal arc hardfacing.
Exceptional resistance in corrosive media at high temperatures, including erosion and thermal shocks.
Ideal for hardfacing parts undergoing the single or combined effects of heavy metal-to-metal wear or abrasion, temperatures ranging from RT to 800°C, impact and corrosive environments.
Precision layer wound for superior wire feeding characteristics.
Extensively used on valve seats of diesel engines, cams, chainsaw bars, hot shear blades, cold forming rolls and hot forming rolls, for hot rolling reinforcing bar, pump parts and components in hot zinc baths etc.
Test Certificates can be found online @wilkinsonstar247.com
Standards |
EN ISO 14700 - T Co2
|
AWS A5.21 - ERCCoCr-A
|
Chemical Composition % (Typical) |
C% |
Mn% |
Si% |
Cr% |
W% |
Fe% |
Co% |
1.05 |
1.00 |
1.00 |
29.0 |
4.50 |
4.00 |
Bal. |
Structure is chromium and tungsten carbides in an austenitic type matrix
|
Hardness (HRC) |
Current Type
|
Hardness - Third Layer |
DC+ / Pulsed |
42
|
Mechanical properties are approximate and may vary based on the heat, welding parameters and other factors.
High Temperature Hardness |
20ºC |
200ºC |
400ºC |
600ºC |
800ºC |
420 Hb |
360 Hb |
330 Hb |
240 Hb |
140 Hb |
High deposition rates and low dilution are facilitated by pulsed current. High heat inputs favour lower hardness. |
Wear Type Suitability |
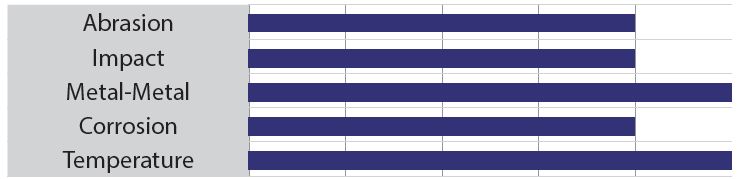
|
Welding Parameters |
Ømm |
Current (A) |
Voltage (V) |
1.20 mm
|
100-250 |
16-29 |
1.60 mm |
140-350 |
16-30 |
Shielding Gases
EN ISO 14175 - I1 (Argon)
Welding Positions
EN ISO 6947 -PA, PB, PC, PD, PE, PF, PG
Packaging Data |
Diameter
|
Weight
|
Spool |
Pallet Qty
|
1.20 mm
1.60 mm
|
15 Kg
15 Kg
|
BS300
BS300
|
72
72
|
Liability: Whilst all reasonable efforts have been made to ensure the accuracy of the information contained, this information is subject to change without notice and can be only considered as suitable for general guidance.